Accelerating the Surgical Glove Supply Chain
The machines supplying healthcare professionals called for an upgrade
A large manufacturer of surgical gloves expanded its production. These sterile rubber gloves intended for use in surgical procedures had to meet exact standards and performance criteria including leak resistance, certain physical properties, and biocompatibility.
To meet this challenge while expanding its enterprise, the firm introduced a unique system involving unique sensors known as thermocouples, ceramic pieces with drilled holes, batteries, radios, and innovative circuitry — all under the guidance of MTSI.
Thermocouples, which are temperature sensors composed of two different metals fused at one end, were installed in one of the gloves. These sensors generated a voltage when exposed to temperature fluctuations, allowing for exact temperature measurement.
To assess and control the temperature variations, we developed a Fortran program to produce a 3D model of the gloves as they moved through various temperature baths. The program utilized false colors to visualize temperature changes, enabling the adjustment of bath temperatures for optimal yield and sterilization, crucial for surgical gloves.
Additionally, a waterproof NEMA IPC-64 box measuring approximately two feet by three feet was employed to protect the electronic components used in this process. The entire procedure took about an hour to complete, emphasizing the substantial scale of the machine involved.
The plant faced challenges during this period. The high demand for gloves, exacerbated by the HIV/AIDS epidemic, prompted the construction of a third building. Yield problems also arose, particularly due to issues with an industrial inkjet printer used to label the gloves with the logo, size, and lot number.
These gloves met exact standards and performance criteria including leak resistance, certain physical properties, and biocompatibility.
This printer, costing around $25,000, suffered from nozzle clogs, requiring the operators to shut off the machines to clear them out, resulting in the loss of an hour’s worth of production every day.
To fix this bottleneck, MTSI implemented an solution by equipping the printer control unit with a microcomputer — assembled to meet robust industrial design standards. This device incorporated a card cage, power supply, and various auxiliary circuits, all of which were resistant to water and hoses. It also featured high-quality connectors.
The control unit featured a rotary switch on the front panel and three LEDs labeled 1-2, 2-3, and 1-3, alongside three printer heads arranged in a triangle. Only two printer heads would be active at any given time. If quality assurance personnel noticed any smearing or issues with the printing on the gloves, they could simply change the switch setting, discard any affected gloves, and resume production without halting the entire machine.
This solution effectively mitigated the costly problem of nozzle clogs on the machines.
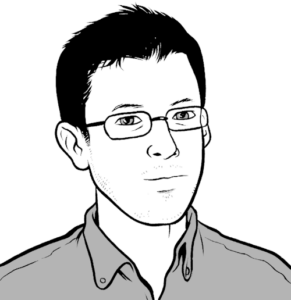
Robert Beckhusen
Robert Beckhusen is a case studies and content marketing editor for Micro Technology Services.